What is 6S?
The 6S methodology is an advanced version of the 5S system, which helps organizations optimize their processes and environments. By integrating Safety into the core principles, 6S addresses not just the physical organization of the workplace, but also the well-being of employees and the prevention of potential risks.
Workplace safety solutions Chennai
6S methodology Chennai
6S implementation Chennai
Enhance workplace efficiency Chennai
6S training services Chennai
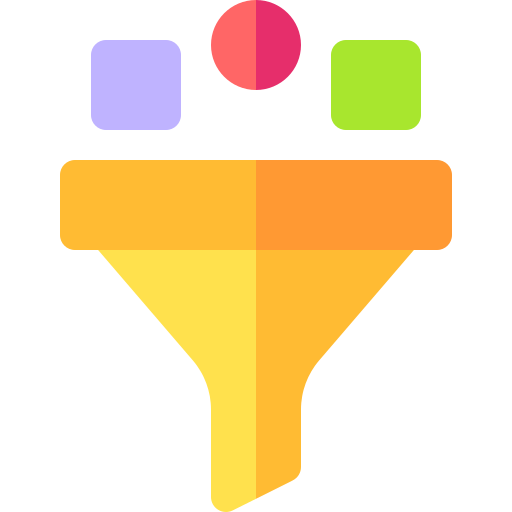
Sort
Remove unnecessary items from the workplace. By decluttering and organizing, you can create a more efficient and safe environment.
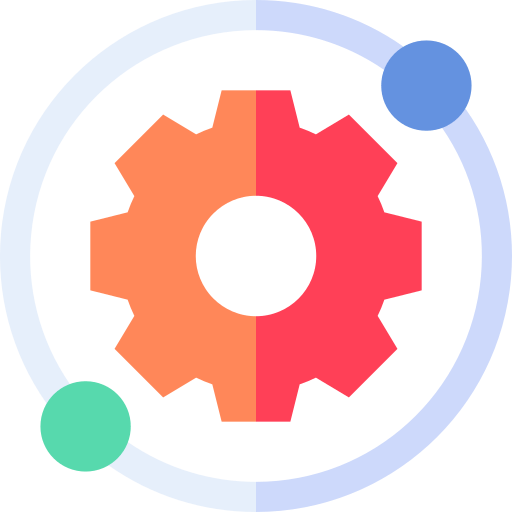
Set in Order
Organize tools, materials, and equipment logically to ensure easy access and efficient workflows. A well-organized workspace improves both productivity and safety.
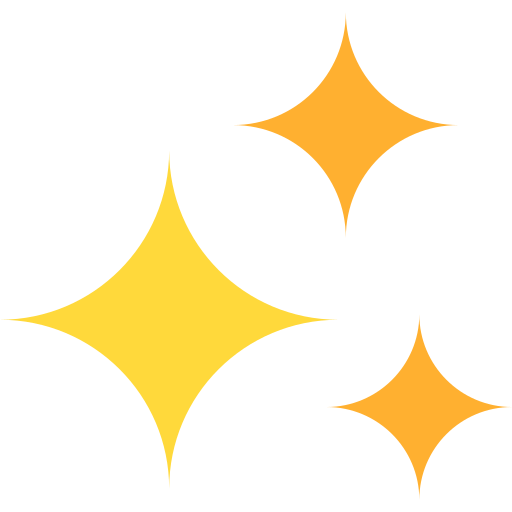
Shine
Maintain a clean work environment to ensure efficiency and safety. Regular cleaning not only enhances productivity but also reduces the risk of accidents and health issues
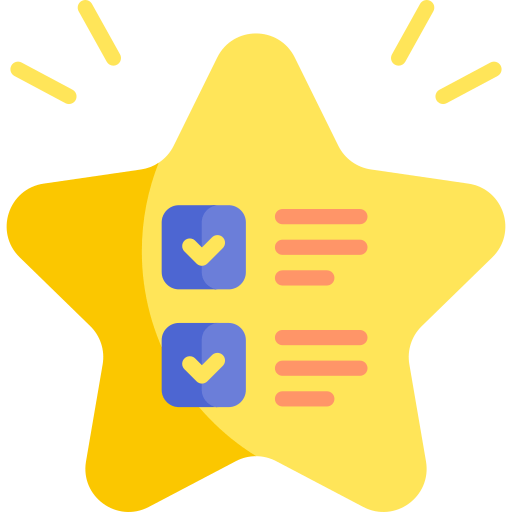
Standardize
Create standardized procedures and practices to maintain the orderliness of the workspace. By implementing consistency across tasks, you reduce the risk of errors and enhance operational flow.
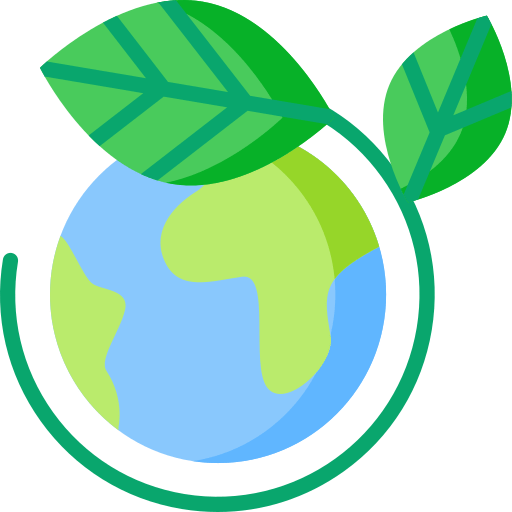
Sustain
Foster a culture of continuous improvement. Sustaining 6S means making these practices part of the daily routine, so the system becomes ingrained in the organizational culture.
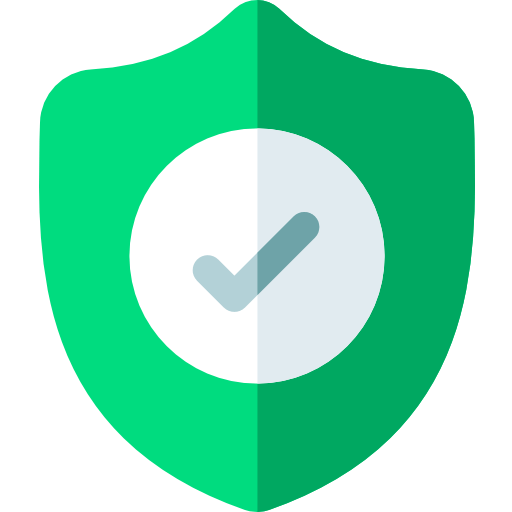
Safety
Prioritize the safety of your employees by identifying potential hazards and eliminating them before they become risks. Regular safety audits, proper signage, and ergonomics are essential components of this step.
Your content goes here. Edit or remove this text inline or in the module Content settings. You can also style every aspect of this content in the module Design settings and even apply custom CSS to this text in the module Advanced settings.
The Importance of Safety in 6S
The Safety element within 6S is not just a consideration – it’s a commitment. Here’s how to integrate safety into your 6S framework
-
Risk Mitigation: Conduct regular safety audits to identify hazards and risks in the workplace. Ensure that employees are aware of potential dangers and know how to address them.
-
Ergonomics: Focus on workplace ergonomics to reduce injuries and discomfort for your employees, improving their overall well-being and productivity.
-
Training and Protocols: Provide ongoing training to employees on safety protocols, emergency response procedures, and best practices to ensure they are prepared for any situation.
-
Protective Equipment: Use proper signage and safety equipment such as helmets, gloves, and other personal protective equipment (PPE) to prevent accidents and injuries.
Workplace safety solutions Chennai
6S methodology Chennai
6S implementation Chennai
Enhance workplace efficiency Chennai
6S training services Chennai
Why Choose Dataspire for 6S Implementation?
Industry-Specific Customization
Whether you’re in manufacturing, healthcare, IT, or another sector, we tailor 6S practices to meet the specific requirements of your industry.
Enhanced Workplace Safety
With safety as a priority, our approach reduces workplace hazards and ensures a safer, healthier environment for your team.
Boosted Productivity
By eliminating waste, organizing resources, and improving processes, we help you optimize your operations and increase overall efficiency.
Sustainable Improvement
We work with you to ensure that the 6S system is sustainable, becoming a natural part of your company culture for long-term success.
Frequently Asked Questions
Why is Safety important in the 6S system?
Safety is a critical element of the 6S methodology. By proactively identifying and addressing workplace hazards, you reduce the risk of accidents, injuries, and health issues. This not only creates a safer work environment but also boosts employee morale and productivity by ensuring workers feel secure.
How do safety audits fit into 6S?
Safety audits are essential for identifying potential hazards in the workplace. Regular audits help detect unsafe conditions such as faulty equipment, hazardous materials, or poor layout design. These audits also ensure that safety protocols are being followed, creating a culture of awareness and vigilance.
What types of safety signage should be used in a 6S system?
Safety signage is an integral part of the 6S methodology to prevent accidents. Key types of signage include
- Directional signs to guide people to safe zones or equipment. These signs help communicate potential risks clearly and effectively, ensuring employees can act safely.
How does ergonomics improve safety in 6S?
Ergonomics plays a significant role in reducing workplace injuries and improving employee comfort. Proper ergonomics ensures that workstations are set up to reduce strain on the body, minimize repetitive stress injuries, and prevent musculoskeletal disorders. In a 6S system, ergonomic principles are applied by adjusting seating, tool placement, and work processes to enhance both productivity and safety.
Can 6S be applied to any industry?
Yes, 6S can be applied to any industry, including manufacturing, healthcare, IT, retail, and services. While the specific implementation may vary, the core principles of organization, cleanliness, and safety are universal and can be adapted to meet the unique needs of any business.